Woolworths: Bridging the gap to distribution efficiency
Innovative bridge and conveyor system enhances connectivity across three buildings.
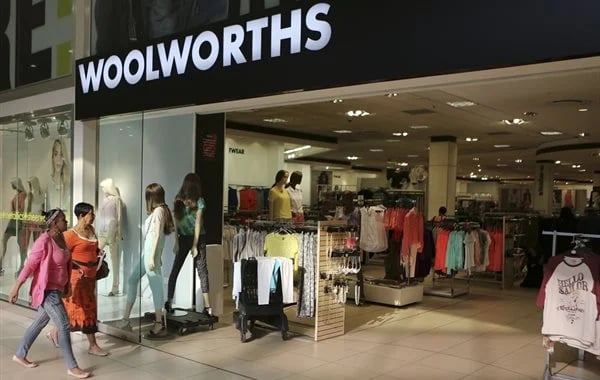
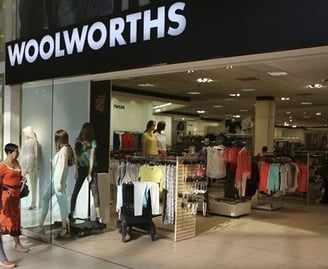
Project Date : 2024
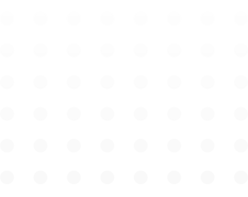
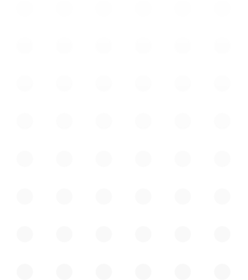
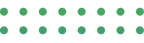
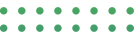
Client Overview
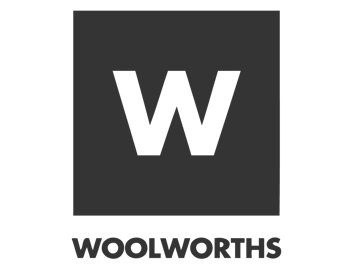
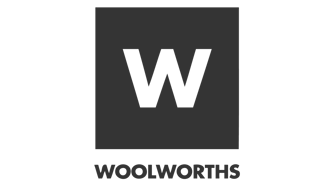
Woolworths, a leading apparel brand in South Africa, required a solution to streamline their distribution processes across multiple buildings at their current national distribution facility in Cape Town. Faced with the challenge of efficiently handling stock replenishment and dispatch across their stores nationwide, Relog assisted with designing and implementing a sophisticated system to connect three buildings, via conveyor bridges. This transformation would allow them to centralize operations and enhance the flow of goods without disrupting ongoing business activities in the DC.
Project Objectives
The project aimed to streamline operational efficiency by centralizing dispatch and stock replenishment systems, especially during stock launches and replenishment periods. This involved designing and implementing a new conveyor layout across multiple buildings, constructing two connecting conveyor bridges to ensure a continuous flow of goods, and centralizing stock storage with an optimized shelving layout to facilitate quicker replenishment to stores nationwide.
The project was executed while maintaining uninterrupted business operations and involved the project manager as the principal agent overseeing the entire project and professional team.
Project Approach
Our team engineered a custom conveyor layout that spanned three buildings, providing a direct link between stock replenishment and dispatch areas.
We oversaw the construction of two bridges that linked these buildings, ensuring a continuous conveyor flow while minimizing disruptions to daily operations.
We assisted the client of the equipment procurement, managing the installation process meticulously to meet the client's strict timelines.
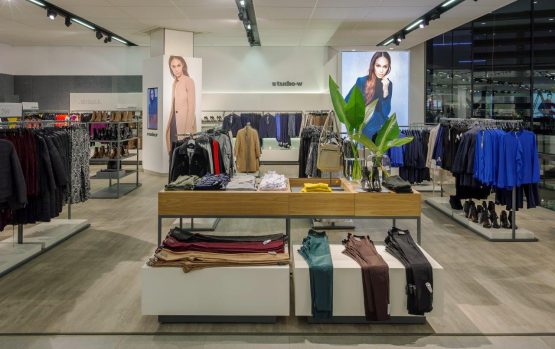
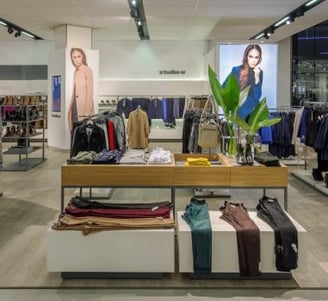
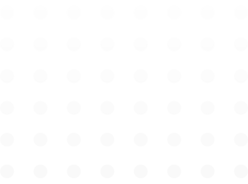
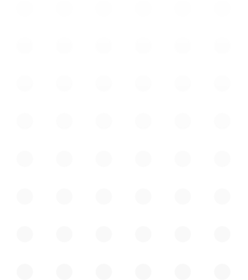
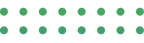
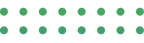
Our team also designed a new shelving system to optimize the storage of replenishment stock, ensuring easy access and improved inventory management.
Throughout the project, the DC remained fully operational, with construction work carefully planned to avoid impacting the client’s downstream business activities.
We led the professional team as the principal agent, coordinating tasks across multiple stakeholders to ensure a smooth execution.
Safety was prioritized, with stringent protocols in place to ensure worker safety and prevent any hazards to ongoing business operations.
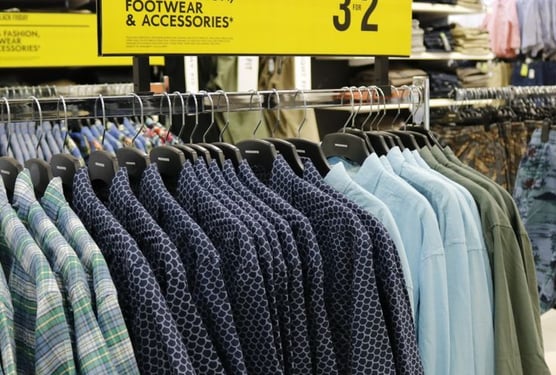
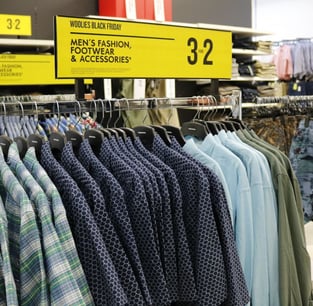
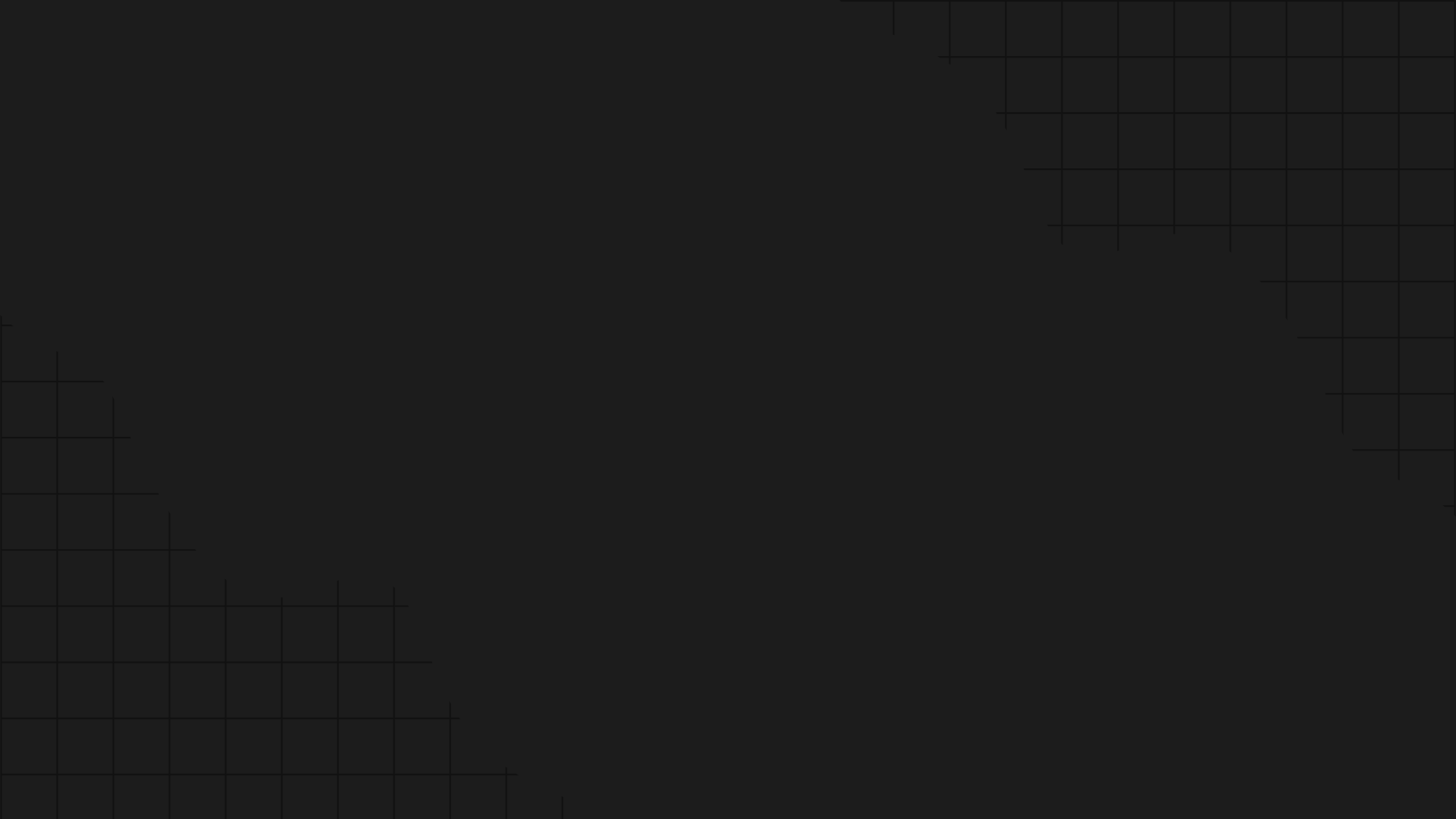
Project Results
The new conveyor layout and shelving system centralized dispatch and replenishment functions, leading to more efficient stock management at stores, as well as distribution.
The bridges created a direct flow between buildings, allowing for seamless movement of goods and reduced bottlenecks.
The project was completed without disrupting ongoing operations, ensuring the client's business activities proceeded smoothly.
The new system enabled faster stock dispatch and replenishment, supporting the client’s growing retail network across South Africa.
The optimized shelving layout provided better utilization of space, improving inventory control and accessibility.
The project was delivered on time and within budget, meeting the client’s expectations for both performance and operational continuity.
This comprehensive solution was also provided to the client with scalable infrastructure that will continue to support their expansion and improve their distribution capabilities well into the future.
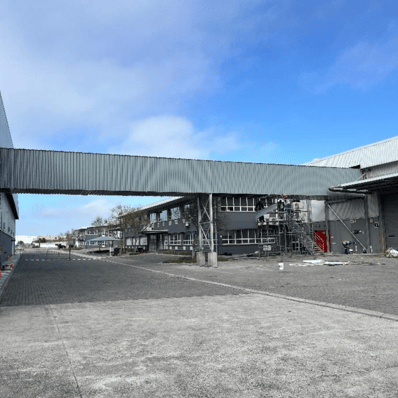
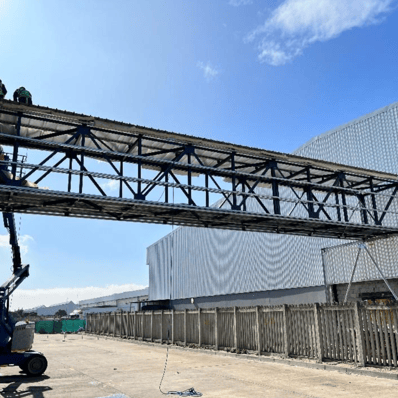
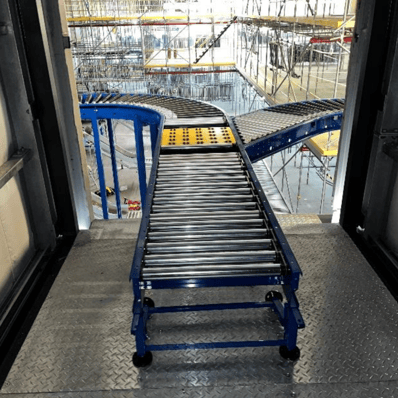