Changing the face of a Kenyan retailer’s value chain
Designing a country-leading warehousing hub to enable Twiga Foods to achieve 10x growth.
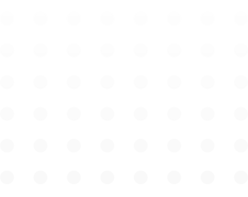
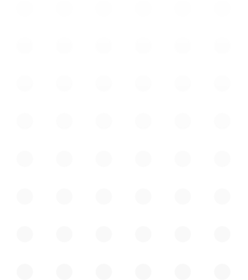
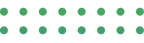
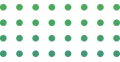
Project Date : 2022
Client Overview
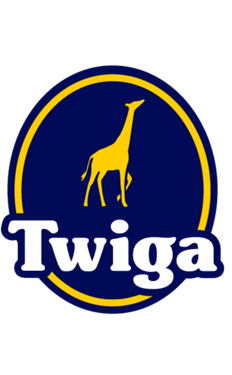
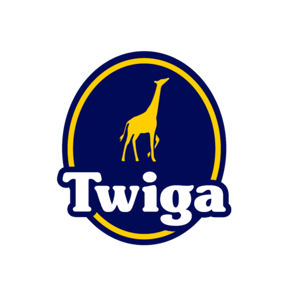
Twiga Foods, a Kenyan-based agri-tech startup, was founded in 2014 with a mission to aggregate informal retail demand and organize an efficient supply chain for fresh and dry goods across urban African cities.
Project Objectives
Due to Twiga Foods' remarkable growth from 2014 to 2019, the company outgrew its informal storage facilities, leading to fragmented operations, inefficient flows, and a lack of operational visibility and quality control.
As a solution, a new 20,000 square meter high-quality warehouse was required to consolidate operations, support future growth, and enhance operational control, visibility, and quality standards.
Project Approach
Meet the team and perform desktop research into the existing business and its history.
Travel to Nairobi, Kenya, to visit the existing storage facilities, their informal depots, and their informal retailers (customers), gain a better understanding of the road infrastructure in Nairobi, and explore potential warehousing options in Nairobi County.
Document existing operational processes and dissect the existing business by analyzing historical data.
Define the design objectives, operational requirements, and budgetary guidelines.
Build several different data models to estimate the required size, capacity, and required capabilities of the various operational needs.
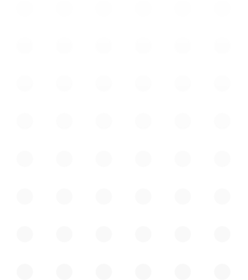
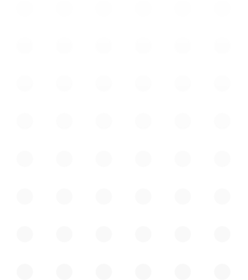
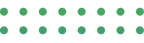
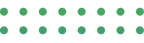
Work closely with the Twiga Foods team to refine the data models, tweak the variables, and agree on design guidelines.
Develop and present several conceptual layouts with different storage solutions and technologies.
Develop detailed drawings of the selected concept design to support the professional team in modifying and upgrading the earmarked warehouse.
Develop end-to-end operational process flows and a WMS FDS (Functional Development) Specification to support the development of a new WMS by Twiga’s competent Operational and IT teams.
Develop and compile the required warehouse equipment specification and tender documentation.
Assist with tender adjudication, supplier appointment, equipment installation, commissioning, training, and handover procedures.
Liaise with the appointed professional team to realize the intended warehouse design.
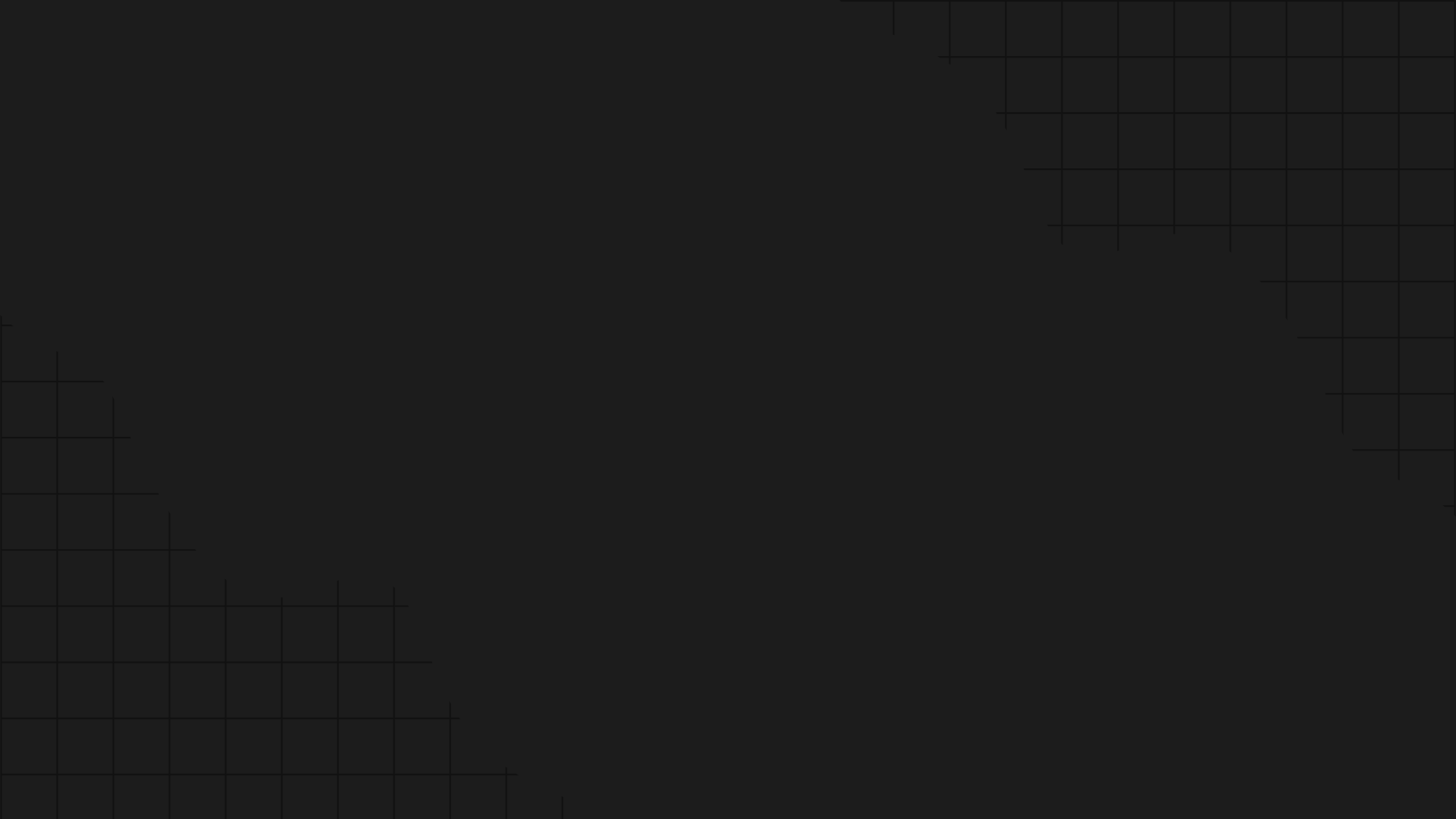
Project Results
The successful go-live of Twiga Foods’ new 20,000 square meters, 14-meter height to eves warehouse.
The ability to efficiently receive, process, store, pick, and dispatch grocery and fresh produce from a centralized fit-for-purpose warehouse.
The ability to receive up to 300 tons of unripe bananas per day through a mechanized banana receiving, checking, and palletizing process.
The ability to ripen and distribute up to 300 tons of bananas daily with Africa's largest fruit-ripening cold rooms (80x 2.4m tall pallets per room).
The development of fully trackable crates equipped with NFC, RFID, and QR codes.
The introduction of 12-meter-high reach trucks into the Kenyan market.
The introduction of radio shuttle technology into the Kenyan market.
The introduction of automated crate washing into the Kenyan market.
The introduction of a centralized, fit-for-purpose, smart battery changeover solution.
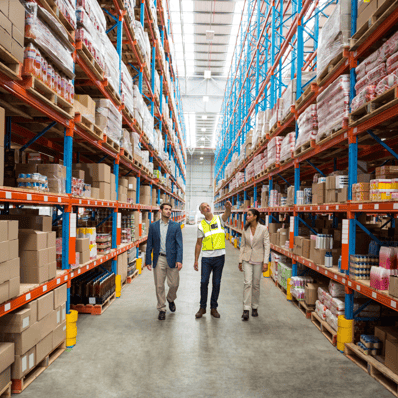
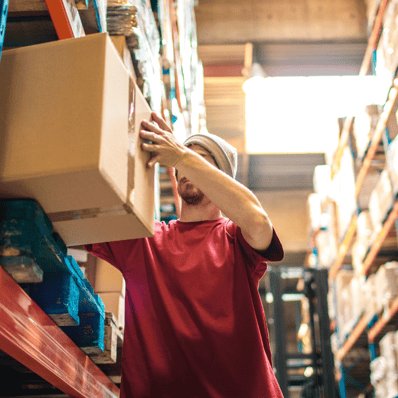
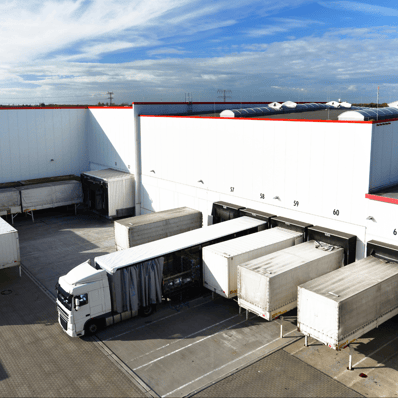
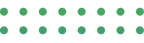
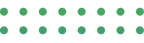
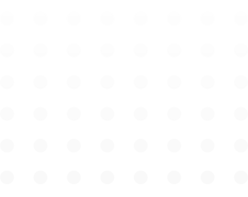
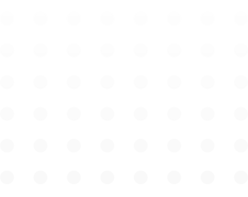
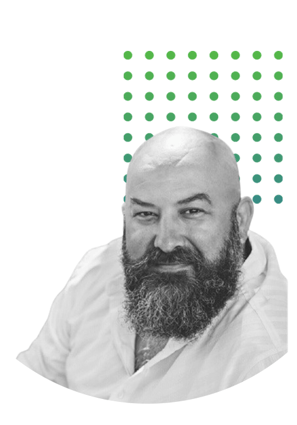
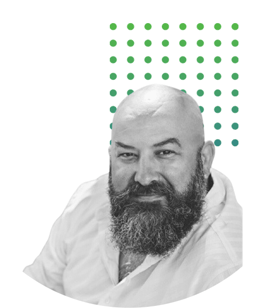
TFG has built a meaningful relationship with the Relog team over the last 2 years. They have been instrumental in the design of our Midrand facility operation to support our strategy for category specific bulk operations, which includes store and eComm fulfilment. It's been great working with the team, and I look forward to our next project!