Creating the freedom to move for a premium South African clothing and apparel brand.
Designing a first-class warehousing solution to enable Freedom Of Movement to quadruple the business in 5 years.
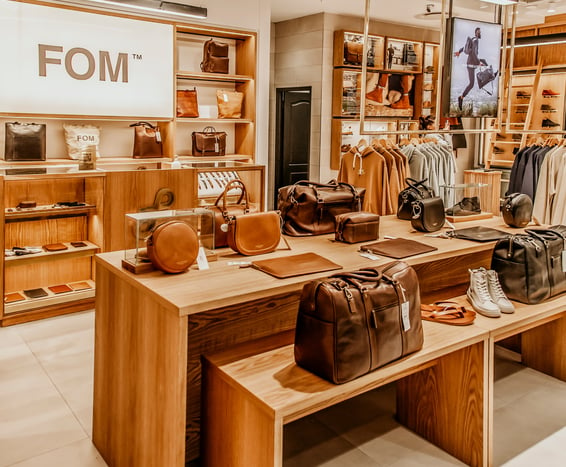
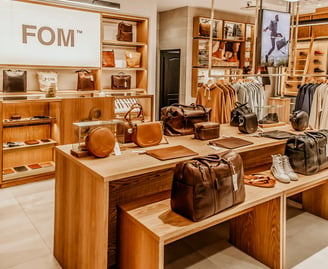
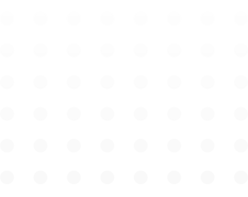
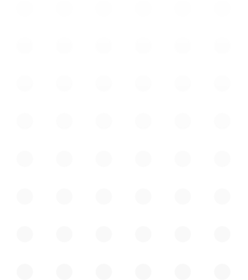
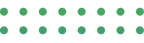
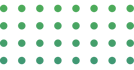
Project Date : 2023
Client Overview
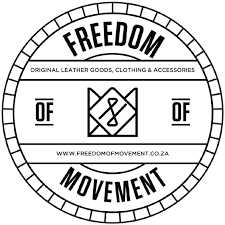
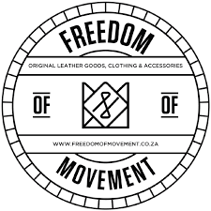
Freedom Of Movement, a proudly South African premium clothing and accessories brand, began its journey in 2013. Founded by the Boezaart brothers in a small room at the University of Stellenbosch, the brand started with just two leather bags. Today, it boasts a collection of over 1,000 premium items and has expanded to 27 stores, truly living up to its name by earning its freedom of movement.
Project Objectives
FOM outgrew the capacity and capability of their warehouse in Woodstock, Cape Town, which limited their volume growth but also led to inefficient flows, lack of operational visibility, and mounting frustrations.
To support their expanding business and improve operational control and visibility, it was clear they needed a new, bigger, and better warehousing solution. This upgrade would help FOM manage operational costs more effectively and continue their growth with greater efficiency.
Project Approach
Visit FOM's current warehouse to understand the product, and document the existing processes and staff needs.
Define design objectives, operational requirements, and budgetary guidelines.
Explore various picking, storage, and operating philosophies, along with potential equipment and technology options.
Develop new operational process flows based on the chosen philosophies and technology levels.
Build data models to estimate the required size, capacity, capabilities, and necessary Full Time Employees (FTEs) to support the new process.
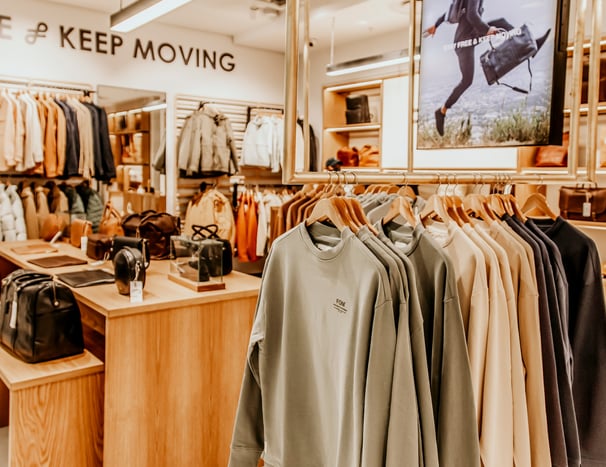
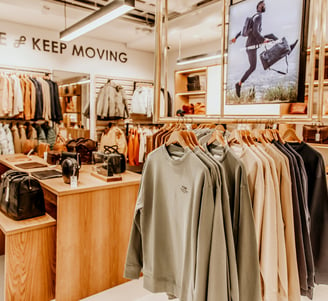
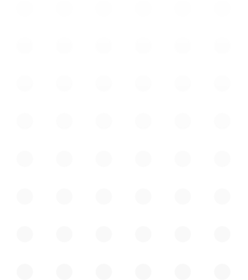
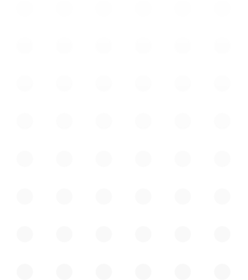
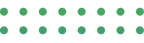
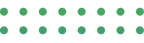
Collaborate closely with the FOM team to refine data models, adjust variables, and finalize design guidelines.
Create and present multiple conceptual layouts with different storage solutions and technologies.
Develop detailed drawings of the selected concept to guide the professional team in upgrading the warehouse.
Compile the required warehouse equipment specifications and tender documentation.
Assist with tender adjudication, supplier appointments, equipment installation, commissioning, training, and handover procedures.
Liaise with the professional team to bring the warehouse design to life.
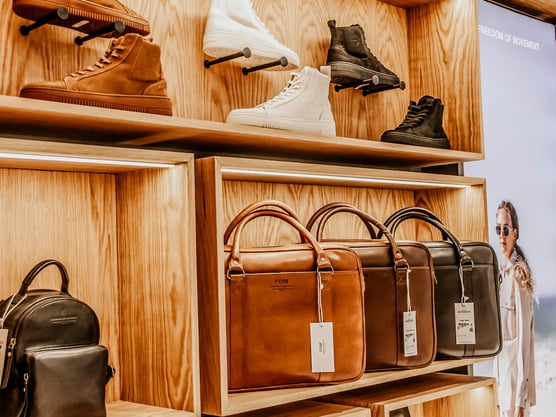
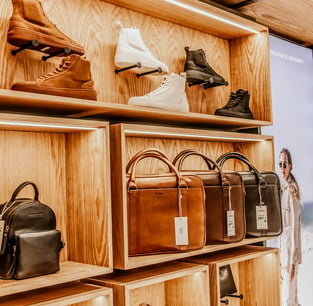
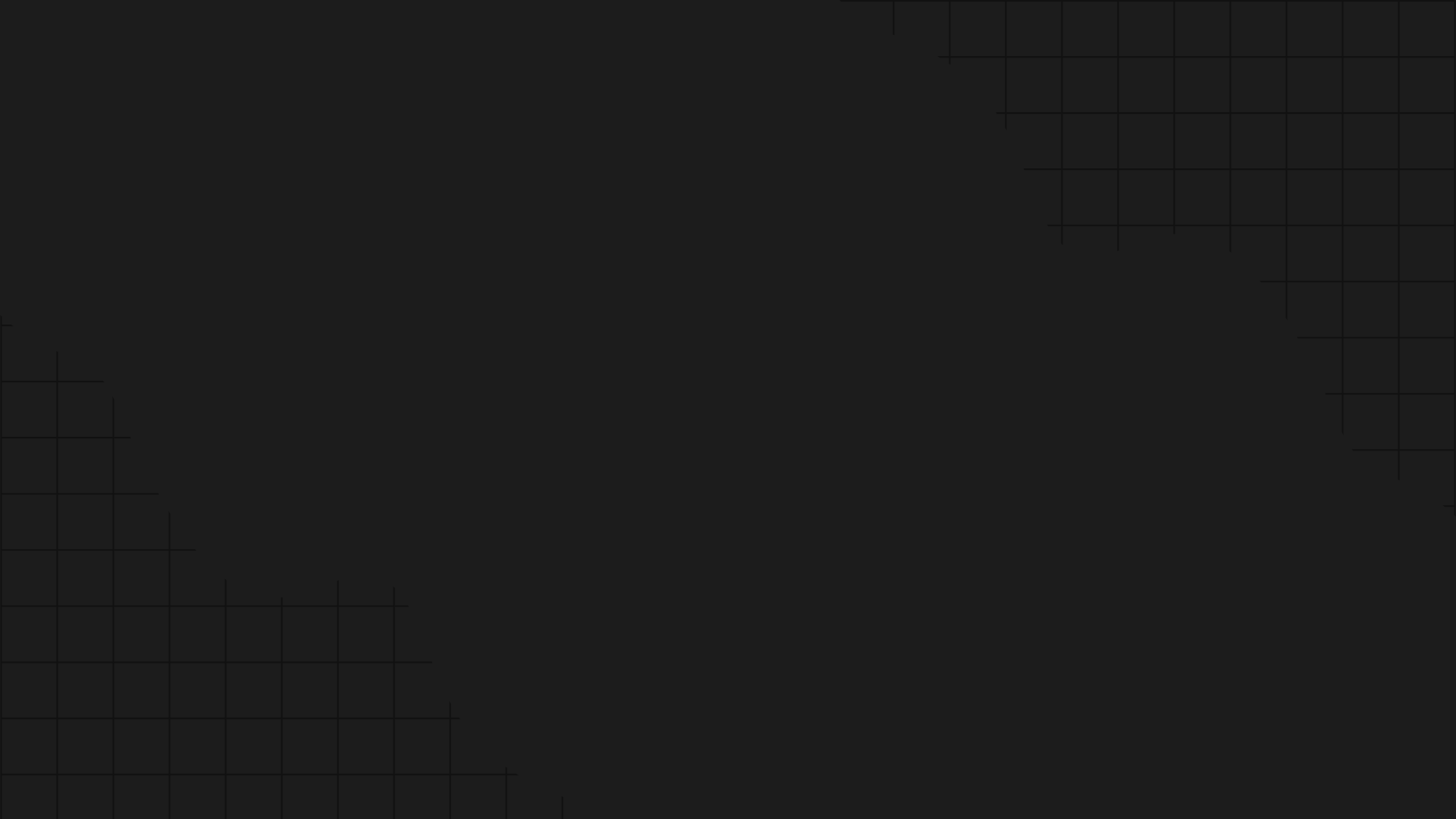
Project Results
Successfully launched FOM's new 1,500-square-meter warehouse with a 9-meter height to eaves, a 900-square-meter storage mezzanine, storage boxes, pick trollies, purpose-built workstations, RFID scan chambers, a dedicated receiving and dispatch floor, and a load-shedding-friendly solution for moving cartons between mezzanine levels.
Ample storage of end-of-season items, stock returns, and consumables within their own facility.
Streamlined processes for receiving, quality control, storing, picking, packing, and dispatching both store and e-commerce orders from a centralized, fit-for-purpose warehouse.
Prepared to implement a sophisticated Warehouse Management System (WMS) over the physical operations when needed.
Developed a 5-year equipment roll-out roadmap.
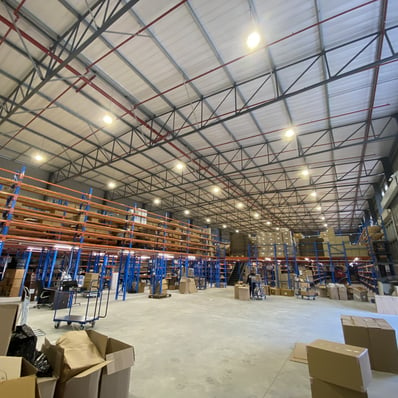
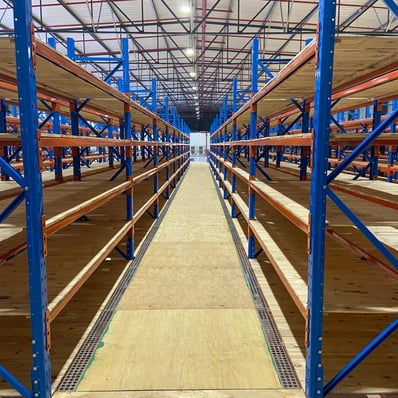
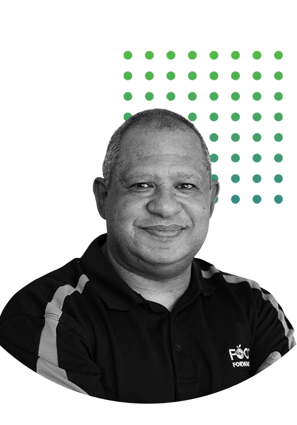
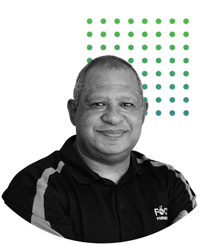
Relog is an integral partner of our work at FoodForward SA. While their professional services are offered pro bono because we are a NPO, their strategic advice, guidance, and design skills around warehousing infrastructure and design, supply chain, inventory flows etc. are remarkable, and have added immense value to our organisation’s operations across the country.